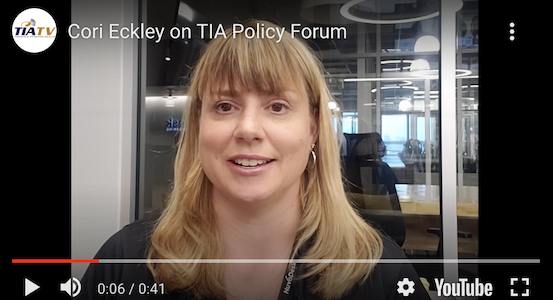
TIA: A Forum for Policy & Action
October 6, 2021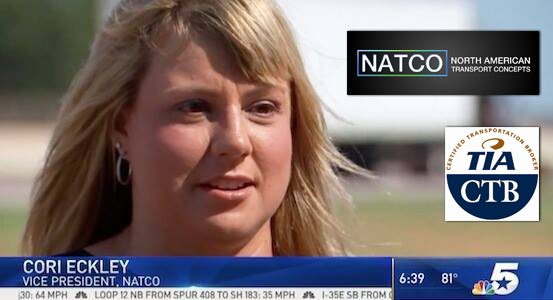
Freight Community
October 21, 2021Or: Floating in Line
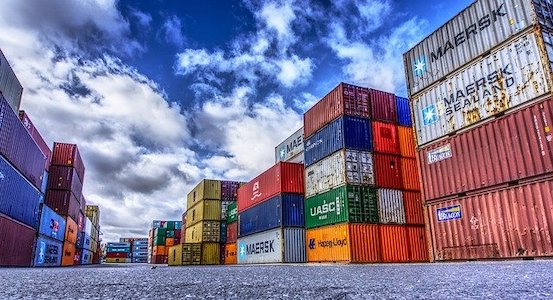
Just Hanging Out
From the As if That Weren’t Bad Enough department: The news lately is filled with stories and images of a global supply chain disruption that has the potential to affect nearly every sector of the country. Empty retail shelves. Delivery delays. Ships backed up for days off the coast of Los Angeles and Long Beach (where some 40% of the nation’s imports arrive). The president encouraging and trying to coordinate a 24-hour-a-day port operation.
NATCO VP Cori Eckley says, “In my years in the industry, I have never seen anything like this.”
What’s going on here?
“Capacity,” says Cori. “It’s called a supply chain for a reason. There’s a domino effect.”
Supply-and-demand. When the pandemic took hold in full force last year, sales tanked. Let’s take computer chips for example. Demand for cars and computers ⏤ which rely on those chips ⏤ plummeted. With drastically reduced demand, computer chip manufacturers curtailed production. As the pandemic eased (and spiked and eased and spiked and eased), demand increased. And now we find ourselves in a situation where supply cannot keep up with demand.
By “supply,” we mean both production and the ability to get things across the ocean, into trucks, to the stores, and into homes.
So, we see all those ships off the coast of California, waiting for the containers stacked in the ports to be trucked away. And there’s a driver shortage. And big box stores are encouraging us to shop now for Christmas. Oh, and Black Friday is going to start way early this year. You read it here first.
Meanwhile, people wait for supplies that sit on ships. The domino effect that Cori speaks of affects other sectors. Drivers negotiate higher rates, citing the higher cost of fuel as a factor. And yes, fuel has shot up recently. Says Cori, “In my years in the industry, I have never seen anything like this.”
It’s not all doom and gloom. NATCO has also taken on overflow for companies that, say, have their own trucks yet can’t get drivers. And, as always, some 50-60% of our loads are managed by picking up the phone and strategically scheduling.
Solid, honest, proactive communication might not make that bottleneck in the Port of Los Angeles magically disappear. And yet, we remain committed to the idea that such communication is essential to a healthy economy.